This content is restricted to registered users only. If you have already registered on the AJP website please login below, Or you can Register for free.
DAA error rates the ‘elephant in the room,’ says MPS
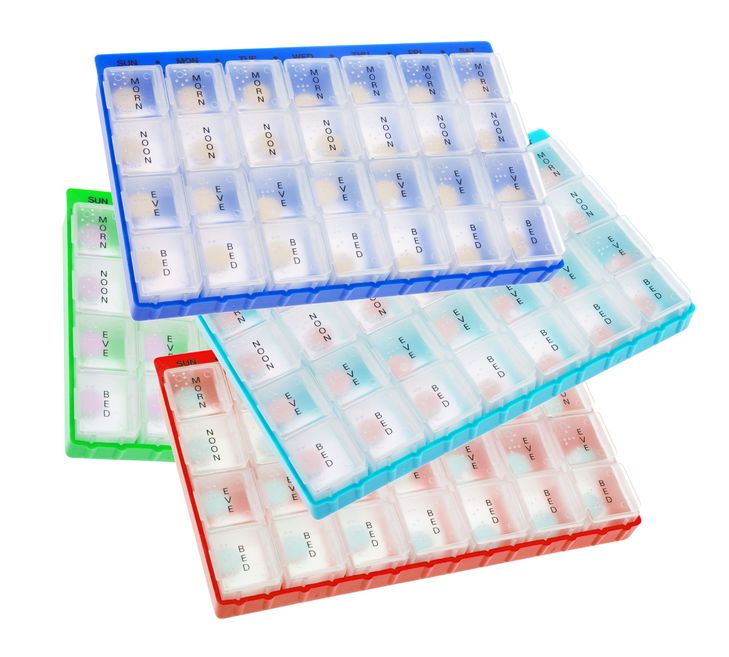
All content on AJP.com.au is restricted to registered users only.
To continue enjoying access to all the news, views, information and education you’ve come to trust, please login & stay in.
And if you don’t already have a login – register now!